Creation of test kits
Even the most effective production process, utilising state-of-the-art machinery, is subject to inherent risks of contamination and defects. Pharmaceutical manufacturers are diligent in their analysis of these risks, adhering to stringent regulatory guidelines. They employ rigorous monitoring procedures to ensure that production standards remain optimal. LabGP offers comprehensive support in the form of risk analysis and characterisation. Our expertise lies in identifying and quantifying the various defects that may arise during production, along with their frequency and typical characteristics.
The creation of representative test kits is important to verify the ability to detect them later in the actual production process.
The defects that can typically occur are as follows:
- Particles of various types, intrinsic or extrinsic to the process, moving in the liquid, floating on the meniscus or attached to the container.
- Container defects, such as cracks, scratches, inclusions, sealing defects, shape defects.
- Contents defects: filling defects, colour or turbidity defects
CONTAINER TYPES
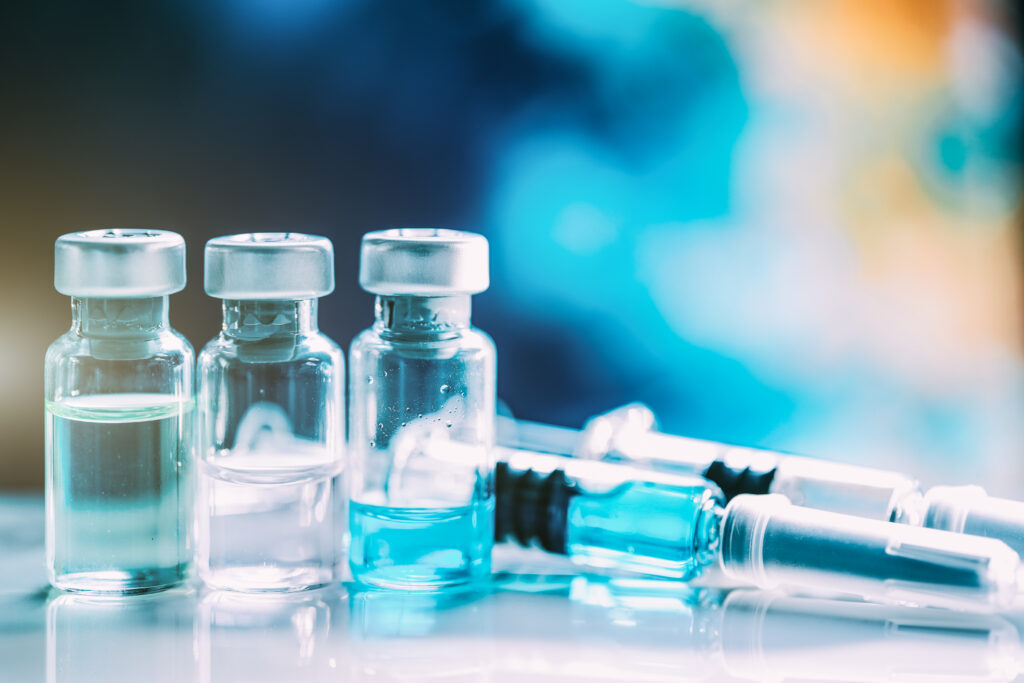
We can provide reference kits for the following container types:
- Prefilled syringes, both in glass and plastic material
- Vials, both in glass and plastic material
- Cartridges
- Infusion bags
- BFS containers
LabGP can work either with containers pre-filled by the customer or by filling the containers directly at our laboratory.
PARTICLE DEFECTS
For the preparation of particle defects, the type and expected percentage of defects is agreed with the customer so that the kit can best represent the production conditions. This is useful whether the kit is used for training manual inspectors, for the creation of a ‘Knapp batch’ or for the initial setup and periodic verification of an automatic inspection machine.
The contaminant materials used to create the particles can be supplied by the customer or taken from the LabGP archive.
The size range of the particles to be included will be defined with the customer according to the type of kit: in the case of a study, even low size values (50 µm) can be used, while in the case of a ‘functional / daily test kit’, higher values (100-200 µm) are preferable. Typically, only one particle is placed in each container. This is always evaluated on the basis of the risk analysis and agreed with the customer.
The kit will be accompanied by a detailed description of each particle inserted, its picture, its dimensional characteristics, a report and a kit certificate.
CONTAINER DEFECTS
The following types of “cosmetic” defects can be generated:
- Fill volume deviations, discolouration or turbidity deviations can be simulated.
An image and characterisation of each defective container is included in a final report. - “Classic” defects such as cracks, scratches and chips on glass; closure defects such as dents or bumps on aluminium seals; improper sealing or raised flip-offs.
- Process-specific defects can also be created (even from sample images if available)
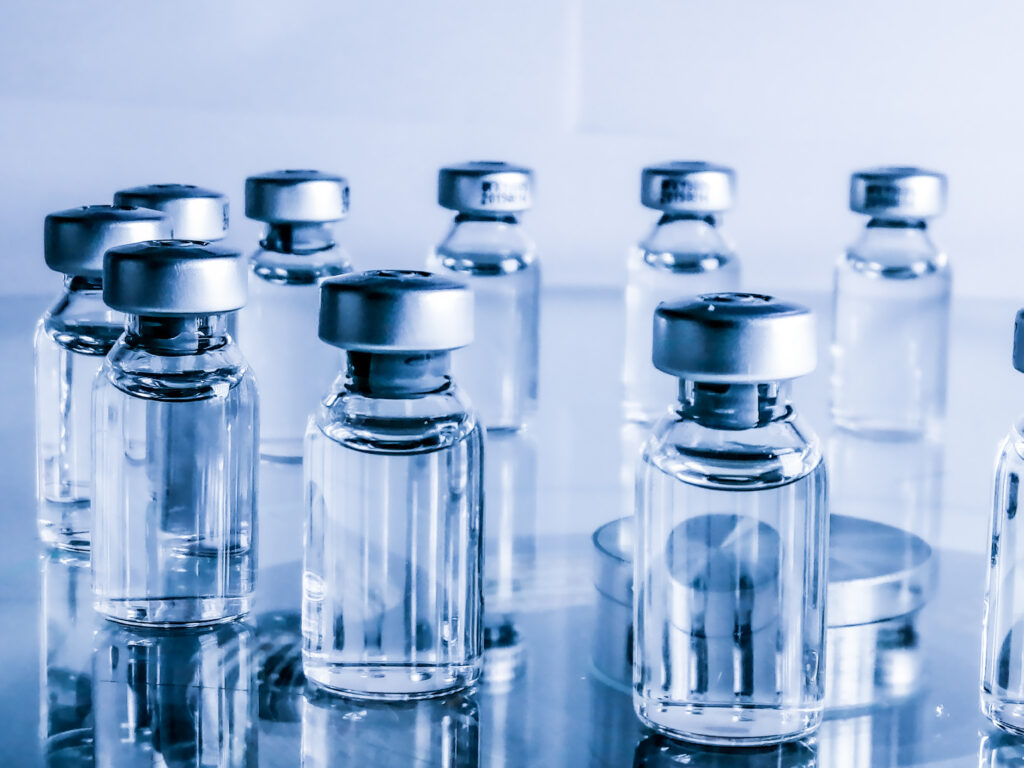
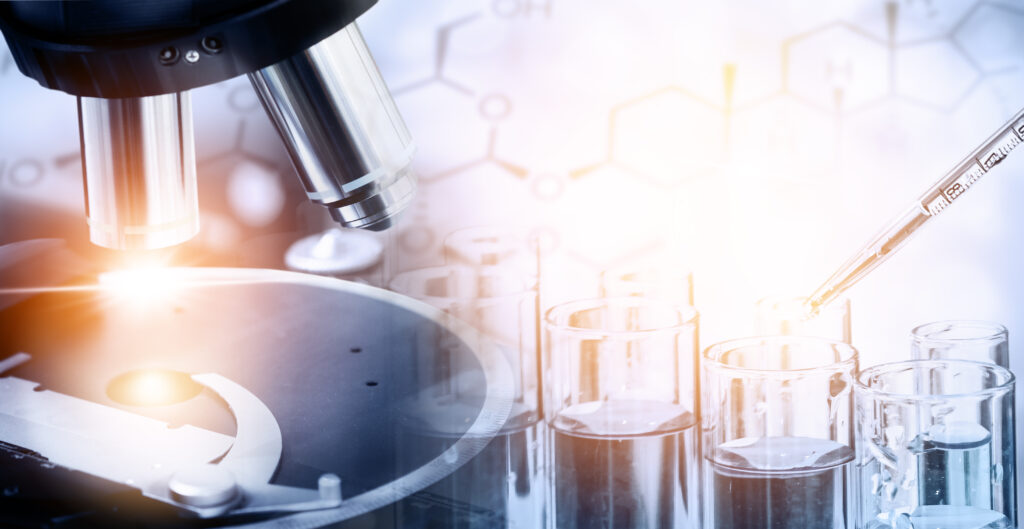
MEDIA FILL
A “media fill” test is a key microbiological test to evaluate the effectiveness of an aseptic manufacturing process. Good Manufacturing Practice (GMP) standards require “media fill” tests to be conducted on a regular basis to verify the microbiological conditions of its own aseptic processes.
LabGP can create kits with different turbidity levels to simulate using standard liquids the final verification process based on media fill.
MICRO-HOLES FOR CLOSURE INTEGRITY TESTING
Checking the integrity of container closures (CCIT) is another key element in the manufacture of sterile pharmaceuticals.
Laser technology can produce holes down to a few microns in almost any material up to 2mm thick. The reference kit used to verify the effectiveness of CCIT equipment must take into account not only the size of the hole, but also its position in the container.
The customer can provide specifications for these parameters or LabGP can suggest a hole position and microhole size range based on previous experience.
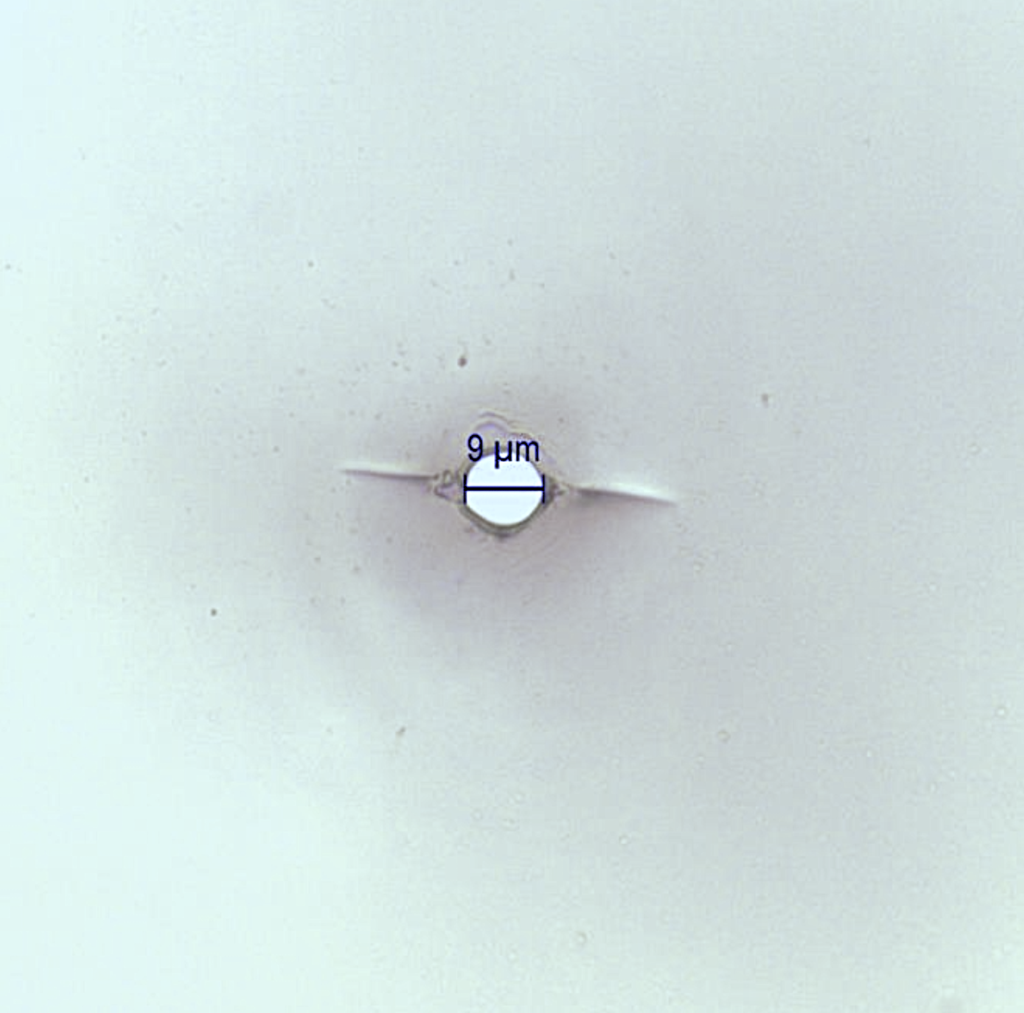